Understanding Work in Progress and Why it Matters
Many businesses struggle with understanding their true value of Work in Progress (WIP). Some struggle with a higher value of Work in Progress than is appropriate for their business.
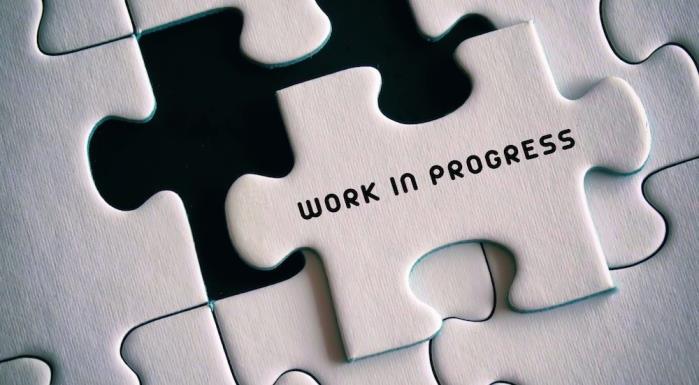
Work in Progress can have major impacts on the financial performance and position of a business, so understanding it and how to manage it is crucial for business performance.
What is Work in Progress?
Simply put, Work in Progress is the value of inventory, labour and overhead of work that is in progress and has not been completed. Work in Progress is an Asset account in the chart of accounts because it is an asset the business owns.
Work in Progress in Manufacturing
In manufacturing there are two meanings to the term Work in Progress, that while closely related, are quite different. If these differences are not made clear in the financials it can cause confusion.
In the manufacturing process raw materials are assembled or processed into finished goods that are then sold. It is during the in-between stage part way through the manufacturing process where the meaning of the term Work in Progress can become blurred. It can be used to mean two things, that should be carefully distinguished.
- Work in Progress is sometimes used to refer to inventory in stock that has been processed to a certain state in the manufacturing process and is awaiting further processing for finished goods inventory to be completed for sale. These are sub-assembly or semi finished products with their own item code that have an on hand quantity and can be counted. It is not uncommon for sub-assembly or semi finished components to be manufactured and held in stock waiting to be used in the manufacture of a number of finished goods products. This is not Work in Progress in the true sense of the term and simply refers to actual inventory in stock at an in between stage between raw materials and finished goods.
- The true meaning of the term Work in Progress is the value of inventory, labour and overhead that have been consumed on production orders in progress for finished goods that have not yet been receipted into inventory. In this case the inventory is not in stock and cannot be counted as it has been consumed for use in the manufacturing process. This Work in Progress refers to the value of inventory, labour and overhead that is the cost of inventory currently being manufactured that is yet to be completed and receipted into stock. This is not part of on hand inventory value as the inventory has been taken out of stock and been consumed.
Both of these relate to the value of inventory assets owned by the business, but the key difference is whether it refers to inventory that is in stock and can be counted, or if it refers to inventory no longer in stock, (plus labour and overhead) that has been consumed on production orders currently in progress.
It is important to distinguish between these as,
- Work in Progress inventory relates to actual inventory value that can be counted and has an on hand value that needs to be reconciled between the on hand inventory value report and the balance of Work in Progress Inventory general ledger account.
- Work in Progress relates to the cost of inventory, labour and overhead consumed on open production orders in progress. Inventory that is work in progress cannot be counted as it is no longer in stock as a raw material or part of a manufactured item. The manufacturing work in progress value report needs to be reconciled with the balance of the manufacturing Work in Progress general ledger account.
To avoid confusion between the two these should be two different general ledger codes with clearly distinguishable account descriptions. We recommend that;
- The General Ledger code for the value of inventory held in stock that is in an in-between state should have a description of “Sub-Assembly Inventory” or “Semi-Finished Inventory”.
- The General Ledger code for the value of inventory, labour and overhead consumed on production orders in progress have a description of “Work in Progress”.
This is important because the value of these accounts will be updated as the manufacturing process flows from raw materials inventory through to semi finished inventory through to finished goods inventory.
Transaction |
Debit |
Credit |
Production Order in Progress |
Work in Progress |
Raw Material Inventory |
Production Order in Progress |
Work in Progress |
Labour and Overheads |
Production Order Completed |
Semi Finished Inventory |
Work in Progress |
|
|
|
Production Order in Progress |
Work in Progress |
Semi Finished Inventory |
Production Order in Progress |
Work in Progress |
Labour and Overheads |
Production Order Completed |
Finished Goods Inventory |
Work in Progress |
Work in Progress for Jobs and Projects
Work in Progress for jobs, whether they be for service, contacting or projects, is the value of inventory, labour and overhead that have been consumed on jobs in progress that have not yet been invoiced.
While these are costs that have been incurred they are not a cost of sale until they are invoiced. Whether job costs should be counted as Work in Progress as an Asset, or Cost of Sales revolves around the matter of ownership and proper reporting in the Profit and Loss.
Job costs are not a cost of sale until the sale has been made and an invoice is been raised to the customer. Until then they are still owned by the business and are therefore an asset. When the job is invoiced to the customer the ownership of the inventory, labour and overhead used on the job passes to the customer and they become a Cost of Sale.
It is only when the sale is recognised by the business that Work in Progress under Assets is posted to a Cost of Goods Sold (COGS) account under Cost of Sales. This is important so that the Profit and Loss report displays the true profit on jobs and reports the business’s true performance.
Transaction |
Debit |
Credit |
Job in Progress |
Work in Progress |
Inventory |
Job in Progress |
Work in Progress |
Labour and Overheads |
Job Invoiced |
Cost of Goods Sold |
Work in Progress |
Job Invoiced |
Accounts Receivable |
Income |
Project jobs may be progressively invoiced over time and the value of Work in Progress for the job at the time the invoice is posted becomes Cost of Goods Sold to date. Varying proportions of job cost to income may result in fluctuations in the proportion of income and cost of goods sold in monthly Profit and Loss reporting.
For example, an invoice may be raised to the job before any work has commenced which would report 100% profit. After materials have been purchased to the job and work has commenced, it is possible that the second progress invoice may have a higher value of job costs than the income on the invoice. This could cause a loss in the Profit and Loss for that month even though the job overall shows a profit.
Some ERP systems, such as Ostendo, can smooth these fluctuations by how Work in Progress is posted to Cost of Goods Sold at the time of invoicing.
Another strategy for managing Work in Progress and Cost of Goods Sold is to hold materials purchased for jobs in inventory and issue them to the job as they are used. Ostendo can reserve stock in inventory for specific jobs.
Cost of Goods Sold (COGS) and Cost of Sales (COS)
It is important to understand the distinction between Cost of Sales and Cost of Goods Sold (COGS) as it relates to work in progress, inventory and job costs.
Cost of Sales is an account type in a chart of accounts along with Assets, Liabilities, Equity and Expenses. Cost of Goods Sold (COGS) is a specific account or subset of accounts within Cost of Sales to record the cost of the sale of assets which is generated when they are invoiced, whether they be inventory in stock or work in progress on a job. In this way the Profit and Loss properly reports the profit of invoiced sales by providing a comparison of the income from invoices and cost of goods sold of those invoices.
The Cost of Sales will include general ledger accounts for other direct costs that relate to sales but are not costs linked to invoices such as rework, warranty costs, labour recoveries and payroll, to name a few. For example, while warranty work is a cost of sale, it is not cost of goods sold because it is not invoiced.
Transaction |
Debit |
Credit |
Inventory Sale Invoiced |
Cost of Goods Sold |
Inventory |
Inventory Sale Invoiced |
Accounts Receivable |
Income |
|
|
|
Job Invoiced |
Cost of Goods Sold |
Work in Progress |
Job Invoiced |
Accounts Receivable |
Income |
How is Work in Progress (WIP) Calculated
In an ERP system, inventory and work in progress values are perpetually being adjusted real time based on actual transactions. The current Work in Progress value of each production order or job can be reported on at any time and compared to the balance of the respective general ledger Work in Progress accounts.
Businesses without an ERP system use opening and closing Work in Progress journals each month to calculate the value of Work in Progress. This is a monthly financial calculation and is not real time, nor does it provide visibility on the Work in Progress value of specific production orders, jobs or projects.
Managing Work in Progress
It is important to manage work in progress so that it is kept at an appropriate level for the business.
A higher value of work in progress than appropriate indicates that too much capital is tied up in unfinished work which in turn indicates that sales have not been realised and therefore profit has not been made. This directly impacts the business in terms of cashflow and profitability.
While there are certain strategies for managing work in progress in the financials, the secret to managing work in progress lies in managing the revenue earning activities of the business which create the work in progress value in the financials.
A higher level of work in progress than is appropriate is usually caused by operational issues such as;
- Data collection for job costing is not timely or inaccurate.
- There are inefficiencies in operational processes causing delays in completing production orders and jobs.
- Production orders or jobs are started without all the required materials being available. This ties up inventory, labour and overhead on partially completed production orders or jobs that are on hold until the shortages of materials are replenished. This inventory, labour and overhead could have been utilised more effectively elsewhere.
- There are too many production orders released to the shop floor, or too many jobs started to be able to be completed in a timely manner with the available resources. This also ties up inventory, labour and overhead on partially completed production orders or jobs that are not being worked on.
- Resources are under utilised or there is a lack of resource capacity which causes bottlenecks. These factors hold up production orders or jobs that are in progress from being completed.
- Projects and jobs are late being invoiced. which means that work in progress value is not converted to cost of goods sold.
Improving planning, efficiencies and the utilisation of resources is the best way to manage work in progress and improve business performance. While Work in Progress can end up being a financial problem, its management very much lies at the coal face of business operations because what happens there creates the figures in the financials.
Using an integrated ERP system, such a Ostendo, with sound operational business processes will give you the information and visibility to manage work in progress and improve business performance